What is Porosity in Welding: Best Practices for Staying Clear Of Permeable Welds
What is Porosity in Welding: Best Practices for Staying Clear Of Permeable Welds
Blog Article
The Scientific Research Behind Porosity: A Comprehensive Guide for Welders and Fabricators
Comprehending the detailed mechanisms behind porosity in welding is vital for welders and makers striving for flawless workmanship. From the make-up of the base materials to the complexities of the welding procedure itself, a plethora of variables conspire to either exacerbate or minimize the existence of porosity.
Recognizing Porosity in Welding
FIRST SENTENCE:
Assessment of porosity in welding exposes vital insights right into the integrity and top quality of the weld joint. Porosity, characterized by the presence of tooth cavities or spaces within the weld metal, is a typical problem in welding processes. These voids, otherwise correctly attended to, can endanger the architectural honesty and mechanical residential properties of the weld, leading to possible failings in the ended up product.

To identify and evaluate porosity, non-destructive testing techniques such as ultrasonic testing or X-ray examination are typically utilized. These strategies allow for the recognition of interior problems without jeopardizing the honesty of the weld. By evaluating the dimension, shape, and distribution of porosity within a weld, welders can make enlightened choices to improve their welding procedures and attain sounder weld joints.
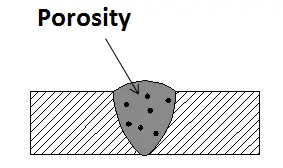
Aspects Influencing Porosity Formation
The occurrence of porosity in welding is influenced by a myriad of aspects, ranging from gas securing performance to the details of welding specification settings. Welding criteria, including voltage, present, take a trip rate, and electrode type, also impact porosity formation. The welding strategy used, such as gas steel arc welding (GMAW) or shielded metal arc welding (SMAW), can affect porosity development due to variations in warm circulation and gas coverage - What is Porosity.
Results of Porosity on Weld High Quality
Porosity formation substantially compromises the structural integrity and mechanical homes of bonded joints. When porosity exists in a weld, it produces gaps or tooth cavities within the material, minimizing the general stamina of the joint. These gaps act as stress and anxiety concentration points, making the weld much more prone to breaking and failure under lots. The presence of porosity additionally deteriorates the weld's resistance to rust, as the trapped air or gases within deep spaces can respond with the surrounding atmosphere, leading to deterioration in time. Additionally, porosity can hinder the weld's capacity to endure pressure or influence, more jeopardizing the overall top quality and integrity of the bonded structure. In crucial applications such as aerospace, automotive, or structural buildings, where safety and resilience are paramount, the harmful effects of porosity on weld high quality can have serious effects, emphasizing the value of reducing porosity with proper welding techniques and treatments.
Methods to Reduce Porosity
Furthermore, using the ideal welding specifications, such as the appropriate voltage, present, and travel speed, is crucial in protecting against porosity. Preserving a regular arc length and angle during welding also assists reduce the chance of porosity.

Making use of the proper welding strategy, such as back-stepping or employing a weaving motion, can click for source also help disperse warmth evenly and reduce the possibilities of porosity formation. By implementing these strategies, welders can effectively minimize porosity and produce top quality welded joints.

Advanced Solutions for Porosity Control
Carrying out innovative innovations and ingenious methods plays an essential role in achieving premium control over porosity in welding processes. Furthermore, using advanced welding methods such as pulsed MIG welding or changed atmosphere welding can likewise help mitigate porosity issues.
Another innovative remedy entails the use of sophisticated welding tools. For example, utilizing equipment Home Page with integrated functions like waveform control and innovative power sources can improve weld top quality and reduce porosity risks. The execution of automated welding systems with accurate control over specifications can dramatically minimize porosity issues.
Moreover, incorporating advanced monitoring and evaluation technologies such as real-time X-ray imaging or automated ultrasonic screening can aid in finding porosity early in the welding procedure, enabling instant restorative actions. Overall, integrating these advanced options can considerably boost porosity control and boost the overall high quality of welded parts.
Verdict
In verdict, recognizing the scientific research behind porosity in visit this site right here welding is vital for welders and producers to produce premium welds - What is Porosity. Advanced remedies for porosity control can further enhance the welding process and make sure a solid and trusted weld.
Report this page